Container
The container is one of the main elements for the performance of the extrusion process. The container mantle has the function of supporting the liner in order to prevent a breakage of the liner under high extrusion pressures. The pressure needs to be distributed homogenously from the liner to the container. And this is possible with a proper shrink fitting process.
Naturally will the shrink fitting constitute a pressure on the container due to the squeezing of the container by the shrink fitted mantle. Finally is this external pressure there in order to balance the generated pressure during the extrusion. The support needs to be continuous and homogenous distributed during the whole extrusion.
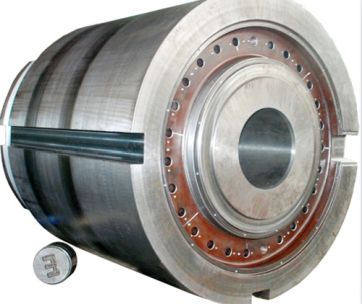
Container Liner
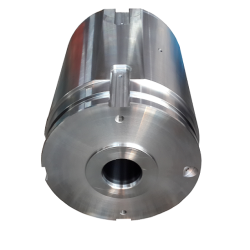
The liner mainly resists during the extrusion against the wearing effects of metals and metal oxides. Preserving the hardness at high temperatures is only possible by decreasing the flexion. That’s why the liner needs the support of the container against breakages.
The mainly material features of the container liner are that it has a high hardness, high resistance, a very low flexibility structure. We suggest AISI H13 (DIN 1.2344) or DIN 1.2367, a derivate of H13, as the container liner material.
Measures For Preventing Damages And Extending The Liner Life Time
- Heat up the liner prior to the usage. A slow heating up (60°C/hour) is recommended.
- Be sure that the pre-heating process doesn’t harm the shrink fitting tightness.
- Provide that the liner remains warm when the extrusion press is not operating.
- Be sure that the container temperature doesn’t exceed the liner temperature.
- Avoid a direct fire contact.
- Do not weld.
- Be sure that the die side contact surface is clean.
The Following Are The Most Frequent Pre-Mature Container And Liner Deterioration Reasons
- Improper pre-heating
- Overheating
- Metal fatigue cracks
- Faulty alignment setting between the container and the stem
- Faulty alignment setting of the tie rod
- Limited bearer space between the liner surface and the die
- Aluminium accumulation on the die surface
- Dent front platen or front plate platen
Preventive Check-List For Containers
- Check the centre adjustment of the press.
- Check the thermocouples at least once a week.
- Check the container on whether there are surface cracks or not.
- Check the container hardness at every liner replacement.
- Grind the container inner surface at every liner replacement.
- Immediately repair when there should be any partial movement of the container should be observed inside the container holder.
- Perform machine cleaning against metal accumulation at the container entrance and exit surfaces.
Advantages of Alumax Extrusion Tooling
- Provides a homogenous alloy flow through the die.
- Decreases operating costs.
- Decreases wastes.
- Decreases waiting times.
- Increases productivity.
- Allows isothermal extrusion.
- Increases life-time.
Extrusion Press Stem
The stem is an element which transfers the power of the main cylinder on the billet like a column. The stem, which must operate without bending and cracking under a high power needs to bear a pressure of up to 120 kg/mm2 depending on the size of the press and the performed application. Therefore, the centering during the operation must be performed properly.
AISI H13(1.2344) is the most frequent used hot tool steel for the stem. This steel is brought to Rockwell C45-50 hardness by applying heat treatment. Maintaining this hardness depends on the consistency of the operating temperature and on avoiding internal stresses.
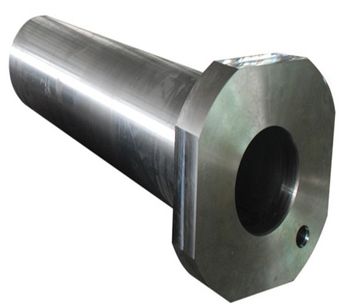